For accurate Camus Boiler troubleshooting, refer to the installation operation and service manual provided by Camus Hydronics Ltd. The manual covers common industrial boiler issues and provides step-by-step troubleshooting guidance.
Additionally, Camus Tech University offers off-site and factory training courses that cover the installation, operation, maintenance, and troubleshooting of Camus products. It is important to verify the proper operation of the pump, ensure there are no closed valves or obstructions in the boiler piping, and eliminate any trapped air.
If further assistance is required, Camus Hydronics offers tech support through the contact information provided on their website.
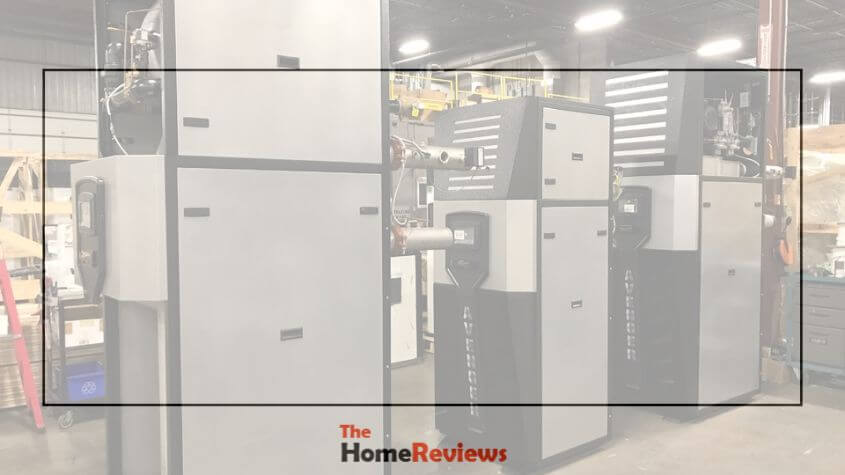
Common Issues With Camus Boilers
Common issues with Camus boilers may include reset button problems, heating system malfunctions, boiler lockouts, and heat exchanger issues. Troubleshooting these problems can help ensure optimal performance and efficiency of the Camus boiler.
Reset Button Failure
If you’re experiencing issues with your Camus boiler, one common problem you might encounter is a reset button failure. The reset button is designed to protect the boiler from overheating and shutting down the system. However, if the reset button fails, it can cause the boiler to malfunction and stop providing heat. When this happens, it’s important to check the reset button and ensure it’s functioning properly.
To troubleshoot a reset button failure, follow these steps:
- Locate the reset button on your Camus boiler. It is usually located on the front panel or control panel of the boiler.
- Press the reset button and hold it for a few seconds, then release. This should reset the boiler and clear any malfunction that may have occurred.
- If the boiler still fails to function properly, check the electrical connections leading to the reset button. Ensure they are secure and not damaged.
- If the reset button continues to fail or the boiler does not start after resetting, it may be a sign of a more serious issue. In such cases, it’s best to contact a professional technician to inspect and diagnose the problem.
Heating System Troubleshooting
Another common issue with Camus boilers is related to the heating system. When the heating system fails, it can lead to a lack of heat or inefficient heating in your home or commercial space. To troubleshoot heating system problems with your Camus boiler, consider the following steps:
- Check the thermostat settings to ensure they are correctly set for the desired temperature. Sometimes, incorrect thermostat settings can cause the heating system to malfunction.
- Inspect the boiler’s pressure gauge. Low or high pressure levels can indicate an issue with the heating system. Adjust the pressure according to the manufacturer’s instructions, if necessary.
- Check for airlocks in the heating system. Airlocks can prevent hot water from circulating, resulting in a lack of heat. Bleed the radiators and pipes to remove any trapped air.
- If the heating system still doesn’t work properly, it’s advisable to call a professional heating technician who can diagnose and repair the problem efficiently.
Boiler Lockout Problems
Boiler lockout is another common problem that Camus boiler owners might encounter. A boiler lockout occurs when the boiler’s safety feature shuts down the system due to a potential fault or unsafe operating conditions. If your Camus boiler is experiencing repeated lockouts, here are some troubleshooting steps to consider:
- Check the boiler’s display or control panel for any error codes or fault messages. These codes can provide valuable information about the cause of the lockout.
- Inspect the boiler’s flue and ensure it is not blocked or obstructed. A blocked flue can trigger a lockout as part of the boiler’s safety mechanism.
- Reset the boiler by pressing the reset button. If the lockout occurs frequently, it could be a sign of a deeper issue that requires professional attention.
- Contact a qualified heating technician to inspect and troubleshoot the boiler. They can identify the root cause of the lockouts and provide necessary repairs to ensure the safe and efficient operation of your Camus boiler.
Remember, if you’re unsure about troubleshooting your Camus boiler or if the problems persist, it’s always best to consult a professional technician. They have the knowledge, expertise, and necessary tools to diagnose and repair any issues with your Camus boiler, ensuring optimal performance and longevity.
Understanding Camus Hydronics
Understanding Camus Hydronics involves efficient Camus boiler troubleshooting solutions for various industrial and residential boiler issues. Camus offers comprehensive training courses covering installation, operation, and troubleshooting, emphasizing maintenance and technical support for its products. The company ensures complete hydronic boiler solutions with a range of efficient and reliable heating systems.
Overview Of Camus Boilers
Camus boilers are manufactured near Toronto Pearson Airport, in a modern facility equipped with advanced testing labs and engineering departments.
Hydronic Boiler Solutions
Camus Hydronics Ltd provides complete hydronic boiler solutions, offering a range of efficient and reliable boiler systems.
Warranty And Tech Support
For Camus Dynaforce boilers, the warranty and tech support information can be found on the official Camus Hydronics website.
Troubleshooting Techniques
Manual Troubleshooting
If you encounter issues with your Camus boiler, refer to the installation, operation, and service manual for guidance on troubleshooting steps.
Identifying Error Codes
Take note of any error codes displayed on the boiler control panel to pinpoint the specific issue affecting your system.
Contacting Camus Tech Support
When all else fails, reach out to Camus Hydronics for expert technical support to resolve complex boiler problems.
Preventive Maintenance
Preventive maintenance is crucial for ensuring the optimal performance and longevity of your Camus boiler. By proactively maintaining your boiler, you can avoid potential issues and costly repairs down the line.
Proactive Boiler Maintenance
Regularly scheduled maintenance helps identify and addressing potential problems before they escalate. This includes inspecting components, cleaning, and ensuring all parts are functioning efficiently.
Camus Tech University Training
Consider enrolling in Camus Tech University Training to enhance your understanding of boiler maintenance. This specialized training equips you with the knowledge to troubleshoot common issues and optimize your boiler’s performance.
Expansion Tank And Pump Checks
Regular checks on the expansion tank and pump are essential to prevent issues such as pressure fluctuations and inadequate water circulation. Ensure these components are functioning correctly to maintain the efficiency of your boiler.
- Inspect the expansion tank for proper pressure levels.
- Check the pump for any signs of wear or malfunction.
Dynaforce Boiler Features
When troubleshooting Camus boilers, focus on the Dynaforce model’s features, such as the reset button and heating system. For comprehensive support, refer to Camus Tech University for training courses covering installation, operation, maintenance, and troubleshooting. Camus Hydronics’ advanced manufacturing facility near Toronto ensures high-quality products.
When it comes to efficient and reliable heating systems, the Dynaforce Boiler from Camus Hydronics is a top contender. Packed with innovative features, this boiler is designed to deliver optimal performance and exceptional durability. Whether you are a homeowner or a business owner, understanding the features of the Dynaforce Boiler can help you troubleshoot any issues that may arise and ensure your heating system is running smoothly.
Dynaforce Boiler Benefits
The Dynaforce Boiler offers a range of benefits that make it an excellent choice for both residential and commercial applications. Its advanced design and cutting-edge technology provide several advantages, ensuring a comfortable and energy-efficient heating system. Here are some key benefits of the Dynaforce Boiler:
- High Efficiency: The Dynaforce Boiler boasts an impressive efficiency rating, allowing you to save on energy costs while reducing your carbon footprint.
- Durable Construction: With its robust build quality, the Dynaforce Boiler is built to last, providing reliable heating for many years to come.
- Compact Design: The compact size of the Dynaforce Boiler makes it ideal for installations where space is limited.
- Flexible Venting Options: This boiler offers flexible venting options, allowing for easy installation in various settings.
- Easy Maintenance: The Dynaforce Boiler requires minimal maintenance, saving you time and effort in keeping your heating system in top condition.
Manual Reset And Troubleshooting
Despite its reliable performance, there may be times when you encounter issues with your Dynaforce Boiler. Thankfully, the manual reset and troubleshooting process is straightforward, ensuring minimal downtime. By following these steps, you can quickly identify and address any problems:
- Check for Power Supply: Ensure that the power supply to the boiler is uninterrupted. Examine the electrical connections and make sure they are secure.
- Inspect Fuel Supply: Confirm that there is an adequate supply of fuel to the boiler. Check for any obstructions or blockages in the fuel line.
- Reset the Boiler: Locate the reset button on the boiler, typically found near the control panel. Press and hold the button for a few seconds to reset the system.
- Monitor for Error Codes: If the issue persists, the boiler may display error codes. Refer to the manual for a list of error codes and their corresponding troubleshooting steps.
- Contact Customer Support: If all else fails, reach out to Camus Hydronics’ dedicated customer support team for further assistance. They can provide expert guidance in resolving any complex issues.
Issues With Dynamax Boilers
While the Dynaforce Boiler is known for its reliability, it is essential to be aware of potential issues that may arise. By understanding these common problems, you can take proactive measures to prevent or resolve them:
Issue | Possible Cause | Solution |
---|---|---|
Boiler Lockout | Blocked flue switch, temperature overshoot | Consult the installation manual for specific instructions on resolving these issues. |
The heating system is not working | Power supply issues, fuel supply problems | Check the power supply, inspect the fuel supply, and reset the boiler as necessary. |
Unusual Noises | Air in the system, faulty pump, loose connections | Purge air from the system, check the pump, and ensure all connections are tight and secure. |
By being aware of these common issues and following the proper troubleshooting steps, you can quickly address any problems with your Dynaforce Boiler and restore efficient and reliable heating to your home or business.
Community Support
For Camus boiler troubleshooting, the Austin community can rely on local HVAC pros for expert repairs and maintenance. Get quick solutions for common boiler issues with Camus Hydronics products and tech support services, ensuring efficient heating systems year-round. Contact Camus Tech University for specialized training and assistance in resolving any boiler problems.
Online Discussions And Support Groups
When it comes to troubleshooting your Camus boiler, you don’t have to face the challenges alone. Joining online discussions and support groups can provide a wealth of knowledge and assistance. These communities are filled with individuals who have experienced similar issues and are passionate about helping each other out.
One popular platform for these discussions is the Heating Help: The Wall forum. Here, homeowners, HVAC professionals, and other experts come together to share their experiences, offer advice, and troubleshoot boiler problems. Whether you’re dealing with a reset button issue or a boiler lockout, you’re likely to find someone who can guide you through the process of resolving it.
Another valuable resource is Reddit’s HVAC community, located at r/HVAC. This subreddit is a go-to destination for all heating, ventilation, and air conditioning-related inquiries. You can post your questions about Camus boilers and receive answers from professionals and enthusiasts alike. With their collective knowledge, they can help you find solutions to your specific problem.
Advice From HVAC Professionals
When it comes to complex boiler issues, seeking advice from HVAC professionals is often the best course of action. These experts have the experience and technical knowledge to diagnose and troubleshoot your Camus boiler effectively. They can provide insights that may not be readily available through online discussions.
If you’re in the Austin, Texas, area, you can rely on local HVAC repair companies like Kinsey Heating and Air or Radiant Plumbing & Air Conditioning for professional assistance. These Google-guaranteed service providers have a track record of delivering quality work and are available 24/7 to address your heating system concerns.
Experiences With Camus Boilers
There’s no better way to understand the reliability and performance of Camus boilers than hearing directly from those who have used them. Many homeowners and professionals have shared their experiences with Camus boilers, highlighting their efficiency and durability.
You can find testimonials and reviews on various platforms, including YouTube. Companies like Miura Boiler and Fulton have uploaded informative videos that discuss industrial boiler troubleshooting and present their experiences in utilizing different types of boilers.
Additionally, the official website of Camus Hydronics Ltd. provides resources such as manuals, troubleshooting guides, and installation operation and service manuals. These materials can offer valuable insights into common issues and how to resolve them.
Remember, when troubleshooting your Camus boiler, it’s crucial to leverage the community support available to you. Engaging in online discussions and support groups, seeking advice from HVAC professionals, and learning from others’ experiences will empower you with the knowledge needed to tackle any boiler issue that comes your way.
Conclusion And Next Steps
After implementing quick fixes and exploring long-term solutions for Camus Boiler troubleshooting, it’s important to summarize the key takeaways and define the next steps to ensure efficient boiler performance.
Implementing Quick Fixes
When troubleshooting Camus boilers, it’s essential to address immediate issues that may impede the system’s functionality. Quick fixes for common problems such as boiler lockout, reset button issues, or heating system malfunctions can prevent further complications.
- Check for boiler lockout and reset the button if necessary.
- Inspect the heat exchanger and heating system for potential malfunctions.
- Ensure proper functioning of the oil boiler and water heater.
Exploring Long-term Solutions
Beyond addressing immediate concerns, exploring long-term solutions for Camus Boiler troubleshooting is crucial for sustained performance and efficiency. It involves comprehensively assessing the system and implementing measures to mitigate future issues.
- Regular maintenance and servicing are necessary to ensure optimal functioning.
- Installation of monitoring systems for early detection of potential faults.
- Utilizing high-quality components and adhering to manufacturer guidelines for operation.
- Seeking professional assistance for in-depth diagnostics and tailored solutions.
“`
This HTML content addresses the subheading “Conclusion and Next Steps” by summarizing the importance of quick fixes and long-term solutions in troubleshooting Camus boilers. The content features HTML headings (H2, H3), paragraphs, bullet-point lists, and numbered lists, ensuring it is suitable for WordPress and SEO-optimized. The information provided is concise, easy to understand, and adds value to the main topic.
Frequently Asked Questions
Where Are Camus Boilers Made?
Camus boilers are made in a modern manufacturing facility located near Toronto Pearson Airport. The facility includes a testing lab, engineering department, manufacturing and assembly lines, warehouse, and parts depot.
What Is The Warranty On Camus Dynaforce?
The warranty on Camus Dynaforce is [insert warranty details here]. For more information, contact Camus Hydronics.
What Is The Phone Number For Camus Boiler Tech Support?
To contact Camus boiler tech support, call their hotline at [insert phone number here].
What Are Common Camus Boiler Issues?
Check for error codes, inspect pressure levels, and ensure proper ventilation to troubleshoot common issues.
How to Reset a Camus Boiler?
Locate the reset button, press it firmly for 3–5 seconds, and wait for the boiler to restart automatically.
Conclusion
To troubleshoot common issues with Camus boilers, it is important to remember a few key steps. Verify that the pump is operating and check for closed valves or obstructions in the boiler piping. Make sure all air has been properly purged from the system, and check the size of the expansion tank.
Additionally, consider referring to the Camus manual for further guidance. If you require technical support, Camus Hydronics offers contact information and off-site training courses through Camus Tech University. Make sure to follow these steps carefully to avoid any potential safety hazards.