Is your Ryobi pressure washer not working? This can be frustrating, especially when you need it most.
A pressure washer is a handy tool for cleaning various surfaces. But like any device, it can sometimes face issues. Ryobi is a trusted brand, known for quality. Yet, even their pressure washers can malfunction. Understanding the common problems can help you fix them quickly.
Whether it’s a loss of power, water flow issues, or strange noises, knowing what to look for is essential. This guide will help you identify and troubleshoot your Ryobi pressure washer problems. Let’s dive into how you can get your pressure washer back in working order.
Common Issues
Ryobi pressure washers are reliable tools for cleaning various surfaces. Yet, like any machine, they can face problems. Understanding common issues can help you troubleshoot and fix your washer quickly. Below are some of the most frequent problems you might encounter.
No Power
One common issue is no power. If your Ryobi pressure washer won’t start, check these areas:
- Ensure the power cord is plugged in.
- Inspect the outlet for power.
- Check the fuse or circuit breaker.
- Examine the power switch for damage.
A faulty power cord can also cause problems. Look for visible damage or wear. Replace it if needed. Also, inspect the motor. If it’s overheating, allow it to cool down.
Low Pressure
Low pressure is another frequent issue. It can make cleaning tasks less effective. Here are some steps to diagnose and solve low pressure problems:
- Check the water supply. Ensure the hose is not kinked.
- Inspect the nozzle for clogs. Clean it thoroughly.
- Examine the pump for leaks. Tighten any loose connections.
- Look at the water filter. Clean or replace it if dirty.
Sometimes, the issue lies with the nozzle size. Ensure you are using the correct nozzle for your task. If the problem persists, the pump might need servicing.
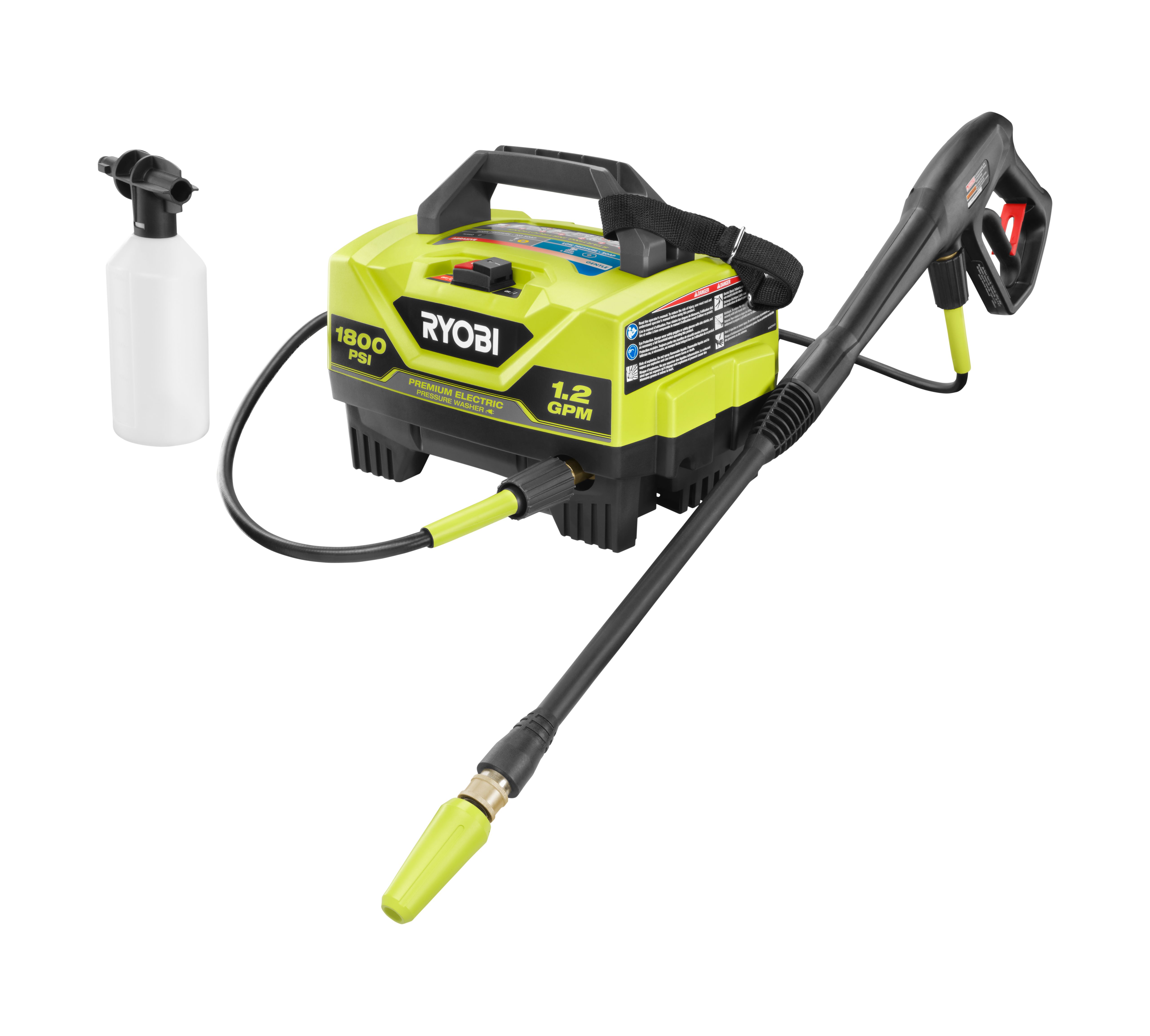
Credit: www.ryobitools.com
Power Supply Problems
Experiencing issues with your Ryobi pressure washer not working can be frustrating. Often, the problem stems from power supply issues. These are easy to check and fix. Below, we’ll guide you through two common areas to inspect: the power cord and the circuit breaker.
Check Power Cord
The power cord is a critical component. Inspect it for any visible damage. Look for cuts, frays, or exposed wires. A damaged power cord can prevent the washer from working.
- Unplug the washer before inspecting.
- Check the entire length of the cord.
- Replace if you find any damage.
If the cord looks good, ensure it is firmly plugged into a working outlet. Loose connections can cause power issues.
Inspect Circuit Breaker
Sometimes, the circuit breaker might trip. This stops power flow to the washer. To check this:
- Locate your home’s main electrical panel.
- Find the breaker controlling the outlet used by the washer.
- If the breaker is tripped, switch it back on.
If the breaker trips again, there might be an electrical issue. Consider calling an electrician for help.
Water Supply Issues
Experiencing water supply issues with your Ryobi pressure washer can be frustrating. Often, the problem lies in the water supply, which is essential for the washer to function properly. Ensuring a steady and adequate water supply can resolve most operational problems.
Check Hose Connection
Start by checking the hose connection. Make sure the hose is securely attached to the pressure washer and the water tap. A loose connection can lead to a reduced water flow or no water flow at all.
- Ensure the hose is tightly connected.
- Look for any visible leaks or damages.
- Replace any damaged hoses immediately.
Even a small leak can significantly affect the performance of your pressure washer.
Inspect Water Source
Next, inspect the water source. Ensure that the water supply is on and delivering adequate pressure. Low water pressure can prevent the washer from working effectively.
- Turn on the water supply fully.
- Check if the water pressure is sufficient.
- Use a pressure gauge to measure the water pressure if needed.
If the water pressure is too low, it might be due to clogged pipes or a malfunctioning water source. Ensure that the water source is not obstructed or restricted in any way.
Sometimes, the problem can be as simple as a kinked hose. Straighten out any kinks to ensure a smooth water flow.
Addressing these water supply issues can often resolve problems with your Ryobi pressure washer. Regular maintenance and checks can keep your equipment running efficiently.

Credit: www.reddit.com
Clogged Nozzles
One common issue with a Ryobi pressure washer is clogged nozzles. Clogged nozzles restrict water flow. This leads to reduced pressure and poor performance. Regular maintenance helps keep your pressure washer in top condition.
Clean Nozzle Tips
Cleaning the nozzle tips is essential. Follow these steps to ensure your nozzles are clear:
- Turn off the pressure washer.
- Detach the nozzle from the spray wand.
- Use a nozzle cleaning tool or a small paper clip.
- Gently insert the tool into the nozzle tip.
- Remove any debris or buildup.
Rinse the nozzle with water before reattaching it. Regular cleaning prevents blockages and ensures optimal performance.
Replace Damaged Nozzles
If cleaning doesn’t work, inspect the nozzle for damage. Damaged nozzles may cause uneven spray patterns or leaks. Replacing damaged nozzles is crucial for the effectiveness of your pressure washer.
To replace a nozzle:
- Turn off the pressure washer.
- Remove the damaged nozzle from the spray wand.
- Install a new, compatible nozzle.
- Ensure the nozzle is securely attached.
Using a new nozzle restores the proper spray pattern and pressure. Always keep spare nozzles on hand for quick replacements.
Pump Problems
Experiencing pump problems with your Ryobi pressure washer can be frustrating. The pump is the heart of your machine. When it fails, the entire system suffers. Let’s dive into common pump issues and how to troubleshoot them.
Check Pump Oil
First, check the pump oil. Low or dirty oil can cause the pump to malfunction. Locate the pump oil reservoir. It’s usually near the bottom of the unit. Use the dipstick to check the oil level. If it’s low, add more oil. Ensure you use the right type. Refer to the user manual for specifics.
Dirty oil can also be a problem. If the oil looks dark or murky, change it. Drain the old oil completely. Refill with fresh oil. This simple step can often fix pump issues.
Inspect Seals And O-rings
Seals and O-rings keep the pump watertight. Over time, they can wear out. Inspect these components closely. Look for cracks or other signs of damage. If you find any, replace them. Damaged seals and O-rings can cause leaks. Leaks reduce the pump’s efficiency.
Replacement parts are usually inexpensive. You can find them at most hardware stores. Follow the user manual for proper replacement procedures. This will ensure your pump works efficiently.
Regular maintenance can prevent most pump problems. Check the pump oil and inspect the seals and O-rings regularly. This will extend the life of your Ryobi pressure washer.
Motor Troubles
Experiencing motor troubles with your Ryobi pressure washer can be frustrating. Without a working motor, your pressure washer won’t function. This section will help you diagnose and fix motor issues. Follow the steps below to get your pressure washer running again.
Inspect Motor Brushes
Start by inspecting the motor brushes. Motor brushes are small carbon parts inside the motor. They conduct electricity. Worn-out brushes can cause motor failure. Remove the motor cover. Locate the brushes. Check for wear and tear. Replace them if they appear worn. New brushes can restore motor function.
Check Motor Windings
Next, check the motor windings. Motor windings are coils of wire inside the motor. They create a magnetic field. Damaged windings can stop the motor from working. To check the windings, use a multimeter. Set the multimeter to the resistance (ohms) setting. Touch the probes to the winding terminals. A reading of zero or infinity indicates a problem. If the windings are damaged, consider getting professional help. Replacing windings can be complex.
Thermal Relief Valve Issues
A Ryobi pressure washer not working can be frustrating. One common issue is with the thermal relief valve. This valve helps maintain safe pressure levels. If faulty, it can affect the washer’s performance. Below are steps to diagnose and fix thermal relief valve issues.
Check Valve Operation
First, locate the thermal relief valve. It’s usually near the pump. Turn off the pressure washer and let it cool. Inspect the valve for any visible damage. Press the valve to see if it moves smoothly. If it sticks, it may need cleaning or replacing.
Replace Faulty Valve
If the valve is damaged, you need a new one. Purchase a compatible thermal relief valve for your Ryobi model. Turn off the pressure washer and disconnect the power. Remove the old valve using a wrench. Install the new valve by screwing it in place. Ensure it’s tight but not over-tightened. Turn on the pressure washer to test the new valve.
Maintenance Tips
Maintaining your Ryobi pressure washer ensures it runs smoothly. Regular care prevents issues and extends its life. Follow these simple tips to keep your pressure washer in top condition.
Regular Cleaning
Clean the pressure washer after each use. Remove dirt and debris from the nozzles. This prevents clogging and keeps the spray strong. Wipe down the exterior to remove grime. Check the hoses for cracks and leaks. Replace them if needed. Clean the air filter often. A clean filter ensures the engine runs efficiently. Inspect the spark plug. Replace it if it looks worn. Regular cleaning helps avoid many common problems.
Proper Storage
Store your pressure washer in a dry place. Avoid damp areas to prevent rust. Drain all water from the pump and hoses. This prevents freezing and damage in cold weather. Keep the pressure washer covered. A cover protects it from dust and debris. Store it in an upright position. This helps maintain its parts in good condition. Proper storage prolongs the life of your pressure washer.
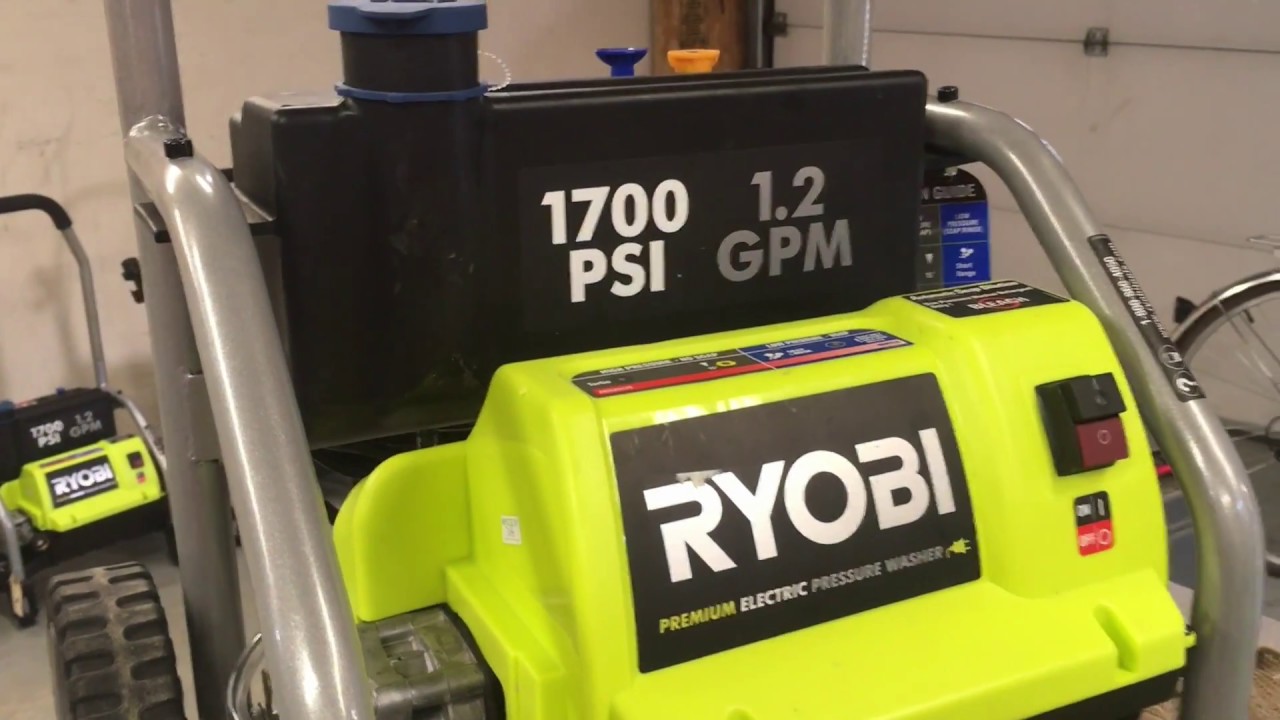
Credit: www.youtube.com
Frequently Asked Questions
Why Is My Ryobi Pressure Washer Not Starting?
Check the power source. Ensure the outlet works and the washer is plugged in securely.
How Do I Fix Low Pressure On My Ryobi Washer?
Clean the nozzle. Clogged nozzles cause low pressure. Check hoses for leaks.
What Should I Do If My Pressure Washer Overheats?
Turn it off. Let it cool down. Check for obstructions or ventilation issues.
Why Does My Pressure Washer Keep Stopping?
It might be overheating or there could be a fuel issue. Check the oil and fuel levels.
How Can I Maintain My Ryobi Pressure Washer?
Regularly clean the nozzle, check hoses for leaks, and change the oil as needed.
Conclusion
Troubleshooting a Ryobi pressure washer can be simple with the right steps. Check connections, hoses, and power sources first. Clean or replace dirty filters. Inspect the nozzle for blockages. Regular maintenance keeps your washer running smoothly. Don’t forget to consult the user manual.
It provides detailed guidance. Proper care extends the lifespan of your washer. Keep these tips handy for future reference. Happy cleaning!