Troubleshooting a Manitowoc Ice Machine often starts with checking the power supply and water inlet. Ensure filters and screens are clean for optimal performance.
Manitowoc Ice Machines are renowned for their reliability and efficiency in producing high-quality ice. Nonetheless, like any sophisticated equipment, they can encounter operational issues. Understanding the common problems and how to address them swiftly can save time and prevent business disruptions.
This guide aims to equip you with essential troubleshooting tips, ensuring your Manitowoc Ice Machine maintains peak performance. With a focus on practical solutions, you’ll learn how to identify and rectify common issues, from minor maintenance tasks to more complex repairs. Keep your ice machine running smoothly with these expert insights, designed to enhance your knowledge and troubleshooting capabilities.
Introduction To Manitowoc Ice Machines
Manitowoc Ice Machines stand as a leading choice for business owners. They offer efficiency and reliability in ice production. Ideal for a range of environments, these machines cater to diverse needs. Restaurants, hotels, and healthcare facilities trust Manitowoc for their ice requirements.
Popularity And Applications
Manitowoc’s popularity stems from their innovative features and consistent performance. The brand’s machines are known for producing ice that’s clear, clean, and compact. This makes them suitable for various applications:
- Food Service
- Hospitality Industry
- Healthcare Facilities
- Education Institutions
Common Models
Manitowoc offers a range of models tailored to specific needs. The Indigo Series is popular for its advanced diagnostics. The Neo Series provides user-friendly operation for smaller setups. Below is a comparison of these common models:
Model Series | Best For | Key Feature |
---|---|---|
Indigo Series | Large Scale Use | Intelligent Diagnostics |
Neo Series | Small to Medium Use | Ease of Use |

Credit: partsfe.com
Symptoms Of Malfunction
Manitowoc Ice Machines are key players in many commercial kitchens. Yet, like all appliances, they can face issues. Recognizing early symptoms of malfunction helps prevent bigger problems.
Unusual Noises
Strange sounds from your Manitowoc Ice Machine may signal trouble. Listen for these:
- Rattling: Loose parts or screws may need tightening.
- Grinding: Worn-out bearings or gears could be the cause.
- Clicking: Electrical components might be failing.
Inconsistent Ice Production
Ice output should be steady. Variations can mean issues:
Issue | Possible Reason |
---|---|
Low Ice | Filter blockages or refrigerant leaks |
Slow Ice Making | Temperature settings or scale buildup |
No Ice | Water supply problems or sensor failures |
Check for these symptoms regularly to keep your machine running smoothly.
Basic Maintenance Checks
Keeping a Manitowoc Ice Machine in top shape is key. Regular Basic Maintenance Checks ensure it runs smoothly. Let’s dive into how to keep your machine clean and efficient.
Cleaning Procedures
Regular cleaning is vital for your ice machine. It prevents mold and ensures fresh, clean ice. Follow these steps:
- Turn off the machine and unplug it.
- Remove all ice from the bin.
- Use a Manitowoc-approved cleaner and follow the instructions on the label.
- Clean all surfaces inside the machine, including the water system.
- Rinse thoroughly with clean water.
- Allow the machine to air dry before turning it back on.
Filter Replacements
Filters play a crucial role in keeping your ice machine clean. They trap dirt and dust. Here’s how to replace them:
- Locate the filter. It’s usually at the front of the machine.
- Turn off the machine.
- Remove the old filter by sliding it out.
- Insert a new filter by sliding it in place.
- Turn the machine back on.
Check your user manual for specific filter model and replacement frequency. Changing filters every six months is a good rule.

Credit: www.yumpu.com
Electrical Issues
Manitowoc ice machines are renowned for their reliability and efficiency. Yet, electrical issues can arise, affecting performance. Identifying and solving these problems quickly is crucial for uninterrupted operation.
Power Supply Problems
Power issues can prevent ice machines from operating smoothly. Here are common symptoms and fixes:
- No power – Check the plug, outlet, and circuit breaker.
- Intermittent power – Inspect the cord for damage. Replace if needed.
- Low voltage – Use a voltmeter to verify outlet voltage. It must meet machine requirements.
Control Board Diagnostics
The control board is the brain of the machine. It requires careful examination when issues occur.
Indicator Lights | Possible Issue | Action |
---|---|---|
Off | Board failure | Reset or replace the board |
Blinking | Error code | Refer to manual for specific code resolution |
Steady | Normal operation | Monitor for consistent performance |
For accurate troubleshooting, refer to the Manitowoc service handbook. It provides detailed guidance on resolving control board issues.
Water-related Challenges
Ice machines need water to make ice, but sometimes they face water issues. Let’s troubleshoot Manitowoc Ice Machines focusing on water-related challenges.
Supply Line Complications
Manitowoc Ice Machines may stop working when water can’t flow in properly. Here are some common supply line problems:
- Kinked hoses can block water from reaching the ice machine.
- Valves that are closed will stop water supply.
- Filters may be clogged, needing a clean or replacement.
Check these parts if your ice machine isn’t getting water:
Part to Check | Action |
---|---|
Hoses | Look for bends and straighten them out. |
Valves | Make sure they’re open. |
Filters | Clean or replace as needed. |
Drainage Obstructions
Water must leave the ice machine too. Blocked drains can cause problems. Here’s what to check:
- Drain lines should be clear of ice and debris.
- Drain pumps need to be functional, not jammed.
Follow these steps to fix drainage issues:
- Inspect the drain line for obstructions.
- Ensure the drain pump is working correctly.
- If needed, clean the line or replace the pump.
Refrigeration Cycle Faults
Having trouble with your Manitowoc Ice Machine? Often, the issue lies within the refrigeration cycle. This cycle cools the water, making ice. If it fails, the machine stops producing ice. Let’s dive into common faults, focusing on coolant levels and compressor performance.
Coolant Levels
The coolant makes your machine cold. Low levels mean warm machines. Check the coolant when the ice isn’t forming right. Signs of low coolant include:
- Less ice production
- Machine takes longer to make ice
- Ice comes out watery
To fix, refill the coolant. Always use the type your machine needs. Not sure? Check the manual.
Compressor Performance
The compressor is the heart of the cycle. It needs to be strong. Weak compressors lead to:
Sign | Meaning |
---|---|
Noisy operation | The compressor struggles. |
High energy bills | It’s working too hard. |
Warm ice | It’s not cooling enough. |
To improve performance, clean the compressor. Remove dust and debris. Ensure airflow is good around it.
Regular maintenance keeps your Manitowoc Ice Machine running smoothly. Always check coolant levels and compressor performance. These steps ensure cold, perfect ice every time.
Sensor And Thermostat Failures
Sensor and Thermostat Failures in Manitowoc Ice Machines can halt ice production. These components are vital for proper machine operation. They ensure ice forms at the right temperature. When they fail, the machine may stop working or produce low-quality ice.
Calibration Techniques
Calibrating sensors and thermostats ensures accurate temperature readings. Follow these steps:
- Turn off the ice machine.
- Locate the sensor or thermostat.
- Use the service manual for specific calibration settings.
- Adjust the component to the correct settings.
- Turn on the machine and observe.
Regular calibration prevents issues and maintains ice quality.
Replacement Tips
If calibration fails, replacement is necessary. Use these tips:
- Choose the correct replacement part.
- Disconnect power before starting.
- Remove the faulty component carefully.
- Install the new part as per the manual.
- Test the machine after replacement.
Use genuine Manitowoc parts for optimal performance.
Professional Repair Or Replace
Manitowoc ice machines are essential for businesses. These machines sometimes need fixes. Knowing when to call a technician or opt for a replacement is crucial. This section helps decide between professional repair or replacement.
When To Call A Technician
Ice machine issues can be complex. Not all problems require a technician. Simple fixes include cleaning filters or resetting the machine. Serious issues need a professional. Signs include:
- No ice production
- Strange noises
- Water leaks
- Error codes
Expertise ensures the machine operates safely and efficiently.
Cost-benefit Analysis Of Repairs
Deciding between repair or replacement involves costs. Consider these factors:
Repair Costs | Replacement Costs | Machine Age |
---|---|---|
Part prices | New unit price | Current lifespan |
Labor fees | Installation fees | Warranty status |
Downtime losses | Upgraded features | Energy efficiency |
Compare repair costs with a new machine’s benefits. Old machines often need more repairs. New machines save on energy and future service costs.
Preventative Measures For Longevity
Preventative measures ensure your Manitowoc Ice Machine runs smoothly for years. Regular upkeep avoids common issues. This guide outlines key steps for machine longevity.
Regular Service Schedules
Like cars, ice machines need regular check-ups. Schedule services with professionals. They spot small problems before they grow. Use this checklist:
- Inspect for wear and tear every 6 months.
- Clean and sanitize components as recommended.
- Replace filters and other parts on time.
Best Practices For Operators
Day-to-day actions impact machine life. Teach your team these best practices:
Action | Benefit |
---|---|
Keep the area clean. | Prevents dust and debris build-up. |
Avoid overfilling. | Reduces strain on mechanisms. |
Handle with care. | Prevents accidental damage. |
Troubleshooting Quick Guide
Welcome to the Troubleshooting Quick Guide for your Manitowoc Ice Machine. This guide is designed to help you quickly identify common issues and implement solutions. Whether you’re facing operational hiccups or performance irregularities, we’ve got you covered with straightforward steps to get your ice machine back to peak performance.
Step-by-step Solutions
Encountering an issue with your Manitowoc Ice Machine can be frustrating. Take a deep breath and follow these steps:
- Check the power supply: Ensure your machine is plugged in and receiving power.
- Inspect for blockages: Clear any visible obstructions in the ice chute or water lines.
- Reset the machine: Sometimes, a simple reset can resolve minor glitches.
- Monitor the error codes: Refer to the machine’s display for specific error messages.
- Clean the unit: Regular cleaning can prevent numerous issues.
When To Refer To The Manual
For more complex problems, the Manitowoc Ice Machine manual is your go-to resource. It contains detailed information and troubleshooting tips for various models. Check the manual:
- After identifying an error code: The manual provides explanations and solutions.
- When routine troubleshooting fails: If initial steps don’t fix the issue, consult the manual for advanced troubleshooting.
- To understand maintenance schedules: Keeping up with regular maintenance can prevent future problems.
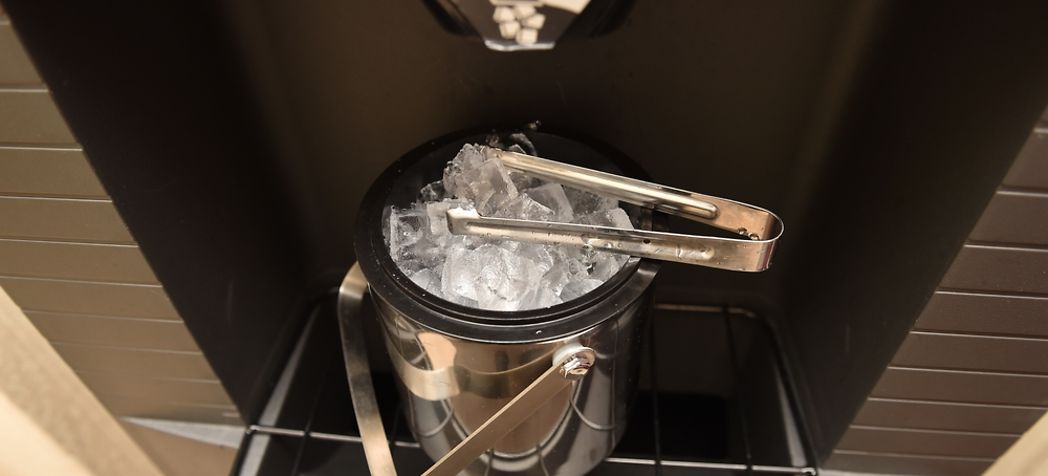
Credit: www.partstown.com
Frequently Asked Questions
Why Is My Manitowoc Ice Machine Not Making Ice?
Manitowoc ice machines may stop producing ice due to water supply issues, clogged filters, or faulty sensors. Ensure regular maintenance for optimal performance.
How Do I Reset A Manitowoc Ice Machine?
To reset a Manitowoc Ice Machine, locate the ‘Off’ button, press it, wait a few seconds, and then turn the machine back ‘On’. Some models may require a specific reset procedure.
What Causes Manitowoc Ice Machine Errors?
Common causes include dirty condensers, water valve failures, low refrigerant levels, or electronic control malfunctions. Regular cleaning and servicing can prevent many errors.
Can I Clean Manitowoc Ice Machine Myself?
Yes, you can clean a Manitowoc Ice Machine by following the manufacturer’s instructions; typically involving cleaning solutions and sanitizers designed for ice machines.
How To Decipher Manitowoc Ice Machine Codes?
Refer to the Manitowoc Ice Machine’s user manual for code descriptions or consult a professional technician for accurate diagnostics and solutions.
Is Manitowoc Ice Machine Maintenance Costly?
Routine maintenance for Manitowoc Ice Machines is generally cost-effective and can prevent expensive repairs. Neglecting maintenance can lead to higher costs down the line.
Conclusion
Wrapping up, troubleshooting a Manitowoc ice machine need not be daunting. With the right approach, most issues can be swiftly resolved. Remember, regular maintenance is key to longevity and optimal performance. For persistent problems, professional help is just a call away.
Keep your machine running smoothly and enjoy the chill!