The Hoshizaki ice machine is beeping due to a technical issue or error. If your Hoshizaki ice machine is beeping, it is likely indicating a problem that needs to be addressed or resolved.
Is your Hoshizaki ice machine beeping? If so, it’s important to address the issue promptly. Hoshizaki ice machines are renowned in the industry for their quality and reliability. However, like any other machine, they may encounter occasional technical problems. The beeping sound is usually an indication that something is wrong and needs attention.
In this article, we will explore some common reasons why your Hoshizaki ice machine may be beeping and provide possible solutions to resolve the issue. By understanding the potential causes and troubleshooting steps, you can get your ice machine back up and running smoothly in no time.
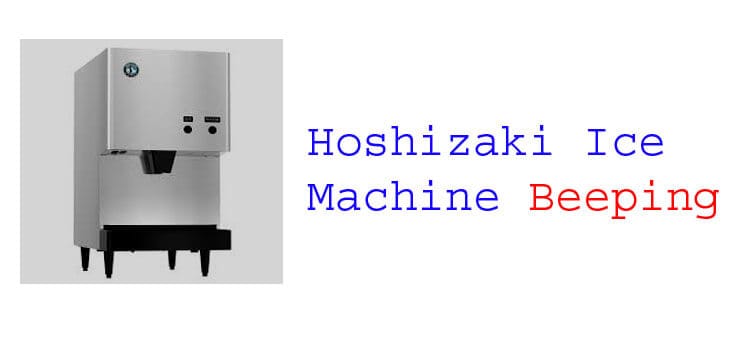
Understanding The Beeping Issue
When it comes to Hoshizaki ice machines, one common problem that many users encounter is the incessant beeping. This is not only annoying but can also disrupt the smooth operation of the machine. To address this issue effectively, it’s crucial to understand the possible causes of the beeping, the importance of addressing it promptly, and the impact it can have on operational efficiency and customer satisfaction.
Possible Causes Of Beeping In Hoshizaki Ice Machines
- Low water level: The beeping in Hoshizaki ice machines can often be caused by a low water level. This can be due to an inadequate water supply or a malfunctioning water inlet valve.
- High ambient temperature: Another possible cause of beeping is a high ambient temperature. When the temperature rises above the optimal range, the machine may start beeping as a warning sign.
- Clogged condenser: A clogged condenser can also lead to beeping in Hoshizaki ice machines. Dust, dirt, or debris accumulation can hinder the heat dissipation process, causing the machine to overheat and trigger the beeping alarm.
Importance Of Addressing The Beeping Promptly
- Preventing system damage: Ignoring the beeping issue can result in severe damage to the ice machine system. Promptly addressing the beeping can help identify and rectify the underlying problem, preventing further complications.
- Avoiding downtime: Unresolved beeping issues can lead to machine malfunctions and subsequent downtime. By addressing the problem promptly, you can minimize the impact on your operation and prevent interruptions in ice production.
- Cost savings: A malfunctioning machine not only affects operational efficiency but can also increase energy consumption, leading to higher utility bills. Resolving the beeping issue in a timely manner can help save on energy costs and prevent potential repair expenses.
Impact Of Beeping On Operational Efficiency And Customer Satisfaction
- Reduced efficiency: An ice machine that continuously beeps can disrupt workflow and reduce overall efficiency. The constant distraction of the alarm can slow down the ice production process and impact productivity.
- Customer dissatisfaction: In a commercial setting, customers expect a constant and reliable supply of ice. A beeping ice machine can signify potential issues and create a negative impression. Promptly addressing the beeping problem ensures that your customers are satisfied with uninterrupted ice availability.
- Reputation management: Customer satisfaction plays a crucial role in building a positive reputation for your business. By promptly addressing the beeping issue and ensuring a smooth operation of your Hoshizaki ice machine, you can maintain a reputation for quality and reliability.
Remember, by understanding the possible causes of beeping, addressing the issue promptly, and ensuring operational efficiency, you can enhance customer satisfaction, minimize downtime, and maintain a seamless ice production process.
Maintenance Checklist: Resolving Common Beeping Causes
Is your Hoshizaki ice machine beeping incessantly? Don’t worry, we’ve got you covered! In this maintenance checklist, we’ll address the common causes of beeping and guide you through resolving them. By following these steps, you’ll be able to troubleshoot and fix any issues with your ice machine efficiently.
Checking For Error Codes On The Control Panel
- Look for error codes displayed on the control panel.
- Understand the meaning of each error code by referring to the manufacturer’s manual.
Verifying Proper Water Supply
- Check if the water supply valve is fully open.
- Ensure that the water supply line is not kinked or twisted.
- Examine the water filter for clogs or debris.
Assessing Water Pressure And Flow Rate
- Verify that the water pressure meets the manufacturer’s recommendations.
- Check the flow rate of water entering the ice machine.
Clearing Any Water Line Obstructions
- Inspect the water lines for any clogs or blockages.
- Use a soft brush or pipe cleaner to remove any debris or scale buildup.
Ensuring Adequate Ice Production And Storage Conditions
- Check if the ice machine is producing ice at the expected rate.
- Ensure that the bin is not overfilled or lacking sufficient ice.
Checking For Ice Machine Cleanliness And Sanitation
- Regularly clean and sanitize the ice machine following the manufacturer’s guidelines.
- Remove any slime or mineral deposits that may have accumulated.
Addressing Issues With Ice Thickness And Formation
- Verify that the water level is set correctly to achieve the desired ice thickness.
- Check for any malfunctions in the ice thickness control mechanism.
Resolving Issues With The Condenser And Evaporator
- Inspect the condenser and evaporator for any damage or leaks.
- Clear any obstructions blocking airflow around the condenser.
Cleaning And Inspecting The Condenser Coil
- Regularly clean the condenser coil to remove dirt and debris.
- Ensure that the coil is not bent or damaged.
Addressing Potential Problems With The Evaporator
- Examine the evaporator for any ice buildup, which could indicate a problem.
- Clean the evaporator thoroughly to remove any scale or deposits.
Troubleshooting Electrical And Mechanical Components
- Inspect electrical connections for loose or damaged wiring.
- Check mechanical components such as fans and motors for proper operation.
Assessing Power Supply And Connections
- Ensure the ice machine is properly connected to a stable power supply.
- Verify that the electrical outlet is functioning correctly.
Examining Control Boards And Microprocessors
- Inspect control boards and microprocessors for any signs of damage or malfunction.
- Reset or replace faulty components as needed.
By following this maintenance checklist, you’ll be able to tackle the common causes of Hoshizaki ice machine beeping. Remember to perform regular maintenance and keep your ice machine in optimal condition to avoid future disruptions.
Advanced Troubleshooting: Expert Tips For Complex Issues
Experiencing issues with your Hoshizaki ice machine can be frustrating, especially when it comes to more complex problems. However, with the right troubleshooting techniques and expert tips, you can address these issues effectively. In this section, we will explore advanced troubleshooting methods for two common problems: the water inlet valve and the refrigeration system.
Addressing Issues With The Water Inlet Valve
The water inlet valve plays a crucial role in the operation of your Hoshizaki ice machine. If you are facing issues related to this component, here are some key points to consider:
- Check the water supply: Ensure that the water supply to the machine is not interrupted and that the water pressure is adequate.
- Inspect for blockages: Look for any obstructions or clogs in the water line that may be affecting the valve’s performance.
- Clean or replace the valve: If the water inlet valve appears to be dirty or malfunctioning, try cleaning it with a mild detergent. If the problem persists, consider replacing the valve with a new one.
Troubleshooting Common Water Inlet Valve Problems
When dealing with water inlet valve problems, consider the following troubleshooting techniques:
- Check for electrical issues: Ensure that there is power reaching the valve. If not, examine the electrical connections and fuses to identify any faults.
- Test the solenoid: The solenoid is an essential part of the water inlet valve. Test it using a multimeter to determine if it is functioning correctly.
- Inspect the valve for leaks: Leaks around the valve can indicate a faulty seal or gasket. Check for any signs of leakage and address the issue accordingly.
Replacing Faulty Valves If Necessary
If troubleshooting and cleaning do not resolve the water inlet valve issues, it may be necessary to replace the valve. Here are the steps to follow:
- Turn off the power: Before beginning the replacement process, cut off the power supply to the ice machine to ensure safety.
- Remove the old valve: Disconnect the water line and electrical connections from the faulty valve. Remove any mounting screws or brackets to take out the old valve.
- Install the new valve: Carefully connect the water line and electrical connections to the new valve. Secure it in place with mounting screws or brackets.
- Test the new valve: Once installed, restore power to the machine and test the new valve to ensure proper functioning.
Dealing With Refrigeration System Problems
The refrigeration system is another critical component of your Hoshizaki ice machine. If you encounter issues with this system, follow these expert tips:
- Checking refrigerant levels: Low refrigerant levels can lead to poor ice production. Monitor the refrigerant levels and recharge if necessary, following the manufacturer’s guidelines.
- Evaluating compressor function: The compressor is responsible for refrigerant circulation. If the compressor is not running or is making unusual noises, consult the manufacturer’s guide or seek professional assistance.
Seeking Professional Assistance When Needed
While many issues can be resolved with the right troubleshooting techniques, it is essential to determine when professional assistance is required. Here are some instances where consulting a Hoshizaki technician is recommended:
- Complex electrical repairs: If you experience electrical issues that go beyond basic troubleshooting, it is best to let a professional handle the repairs to ensure safety and proper expertise.
- Advanced refrigeration system problems: If you are unable to diagnose or fix complex issues with the refrigeration system, it is advisable to seek professional assistance to avoid further damage.
Understanding When To Consult A Hoshizaki Technician
Knowing when to contact a Hoshizaki technician can save you time, money, and potential frustrations. Consider the following situations where professional help might be necessary:
- The issue persists despite thorough troubleshooting efforts.
- The warranty is still valid, and repairs should be handled by authorized technicians to maintain coverage.
- Complex repairs, such as refrigerant leaks or compressor failures, require specialized knowledge and equipment.
Communicating Effectively With Service Professionals
When reaching out to service professionals, effective communication is key. Ensure a smooth and productive interaction by following these guidelines:
- Describe the issue clearly: Provide accurate details about the problem, its symptoms, and any steps you have already taken to address it.
- Ask relevant questions: Seek clarification about the troubleshooting process, estimated repair time, and associated costs.
- Follow instructions: Follow the technician’s recommendations regarding further troubleshooting or necessary repairs.
By adhering to these expert tips and keeping open lines of communication with technicians, you can address complex issues with your Hoshizaki ice machine efficiently and effectively.
Preventive Measures: Avoiding Future Beeping Incidents
Ice machines are an essential part of any commercial kitchen or business that requires a steady supply of ice. However, the constant beeping of an ice machine can be disruptive and frustrating. To avoid future beeping incidents and ensure smooth operation of your Hoshizaki ice machine, it is important to implement preventive measures.
By following these simple practices, you can minimize the risk of beeping and keep the machine running efficiently.
Implementing Regular Cleaning And Maintenance Routines
Regular cleaning and maintenance are crucial for the smooth functioning of your ice machine. By incorporating these routines into your schedule, you can prevent potential issues and extend the lifespan of your machine. Key points to consider include:
- Cleaning the ice machine regularly, including the bin, dispensing area, and other components, to remove any buildup of dirt, debris, or scale deposits.
- Performing routine maintenance tasks, such as lubricating moving parts and inspecting water filters, to ensure optimal performance.
- Following the manufacturer’s guidelines for cleaning and maintenance, as neglecting these can result in the machine malfunctioning and beeping.
Importance Of Scheduled Cleanings And Descaling
Regular cleanings and descalings play a vital role in preventing beeping incidents and maintaining the quality of ice produced by your Hoshizaki ice machine. Here’s why scheduled cleanings and descaling are important:
- Avoiding mineral deposits: Over time, minerals from the water can accumulate inside the machine, leading to scale buildup. Regular descaling helps remove these deposits and prevents beeping caused by poor water flow.
- Maintaining ice quality: Cleanings remove any impurities that may affect the taste and quality of the ice. It ensures that your customers receive clean and fresh ice, reducing the chances of complaints or beeping incidents.
Proper Storage And Handling Of Ice Machine Components
Proper storage and handling of ice machine components can prevent issues that may result in beeping. Here are some important points to keep in mind:
- Store the ice scoop and other accessories separately from the ice, in a clean and sanitary location.
- Handle the ice machine components with care, avoiding any forceful or rough handling that may damage the parts.
- Regularly inspect and replace any worn-out or damaged components to maintain the efficiency of the machine.
Monitoring Ice Machine Performance And Indicators
Regular monitoring of ice machine performance not only allows you to catch potential issues early but also helps prevent beeping incidents. Consider the following:
- Pay attention to any unusual noises, vibrations, or changes in ice production. These may indicate a problem with the machine and should be investigated promptly.
- Keep an eye on the various indicators on the machine, such as low water or low ice alerts. Address these issues promptly to avoid any beeping.
Paying Attention To Temperature Readings
Temperature readings are important indicators of the ice machine’s performance and can help prevent beeping incidents. Keep the following in mind:
- Monitor the temperature of the ice machine regularly to ensure it stays within the recommended range.
- Address any temperature fluctuations promptly, as they may signal a problem that could lead to beeping.
Identifying Warning Signs Of Potential Issues
Being able to identify warning signs of potential issues can help you take proactive measures to prevent beeping incidents. Look out for:
- Water leaks around the machine or unusual water levels in the bin, which may indicate a problem with the water supply or drain system.
- Ice that is discolored or has an unusual odor, as this could point to a contamination issue.
- Any changes in ice texture or shape, which may suggest a problem with the ice-making process.
Training Staff Members On Basic Troubleshooting
Empowering your staff members with basic troubleshooting knowledge can prevent minor issues from escalating and causing beeping incidents. Consider:
- Providing training on how to troubleshoot common problems, such as a clogged water line or a full ice bin.
- Equipping your staff with the necessary tools and instructions to handle minor issues promptly.
Empowering Employees To Handle Minor Issues
By empowering your employees to handle minor issues themselves, you can prevent unnecessary beeping incidents. Here’s how:
- Clearly communicate protocols for reporting and addressing minor issues.
- Provide troubleshooting guides or manuals to help employees identify and resolve simple problems.
- Encourage a proactive approach to maintenance and problem-solving.
Establishing Clear Protocols For Reporting Problems
To prevent beeping incidents, it is important to establish clear protocols for reporting problems. Consider the following:
- Create a system for employees to report any issues they encounter promptly.
- Assign responsibility to individuals who will be in charge of addressing reported problems in a timely manner.
By implementing these preventive measures, you can significantly reduce the chances of your hoshizaki ice machine beeping. Maintaining regular cleaning and maintenance routines, monitoring performance indicators, and empowering your staff to handle minor issues will ensure a smooth and uninterrupted operation of the machine, providing you with a steady supply of ice without the annoyance of frequent beeping.
Frequently Asked Questions Of Hoshizaki Ice Machine Beeping
Why Is My Hoshizaki Ice Machine Beeping?
The beeping sound is usually an indication of a problem or error in the ice machine’s operation.
What Could Be Causing The Beeping Sound From My Hoshizaki Ice Machine?
The beeping sound could be caused by various issues such as a sensor malfunction, a low water level, or a high ice machine temperature.
How Can I Troubleshoot The Beeping Issue On My Hoshizaki Ice Machine?
To troubleshoot the beeping issue, you can start by checking the water supply, cleaning the condenser, and inspecting for any blocked vents or drains.
Can I Fix The Beeping Problem On My Hoshizaki Ice Machine By Myself?
Yes, you can try to fix the beeping problem yourself by following the troubleshooting steps outlined in the user manual or contacting customer support for assistance.
When Should I Seek Professional Help For My Hoshizaki Ice Machine’S Beeping Issue?
If you have performed the troubleshooting steps and the beeping issue persists, it is recommended to seek professional help from a certified technician to diagnose and repair the problem.
Conclusion
To sum up, a hoshizaki ice machine beeping can be a cause for concern, but with the right troubleshooting steps, it can easily be resolved. Start by checking the machine’s water supply and ensuring it’s not blocked or turned off.
Next, inspect the condenser and clean it if necessary to ensure optimal performance. Additionally, ensure that the ice bin is not overfilled, as this can also trigger the beeping. If the issue persists, consult the user manual or reach out to a professional technician for assistance.
Regular maintenance and cleaning of the ice machine can prevent future beeping issues and prolong its lifespan. Remember, addressing the problem promptly will ensure uninterrupted ice production, allowing your business to continue serving refreshing drinks to satisfied customers. So, don’t panic when faced with a beeping hoshizaki ice machine.
Instead, follow these troubleshooting steps to get it back to producing ice in no time.