Liftmaster gates are known for reliability. But sometimes, they may face issues.
Having a Liftmaster gate can make life easier and more secure. But what happens when your gate stops working? Troubleshooting these gates can seem tricky, especially if you’re not a tech expert. This guide aims to simplify the process. Whether your gate won’t open, is stuck, or makes strange noises, we have you covered.
We’ll discuss common problems and practical solutions. This way, you can get your gate working smoothly again without stress. So, let’s dive into the world of Liftmaster gate troubleshooting and solve those pesky issues.
Introduction To Liftmaster Gates
Liftmaster gates are popular for securing properties. They offer convenience and safety. These gates operate smoothly with advanced technology. Many users trust Liftmaster for reliable performance. They come in various styles to match different needs. Liftmaster gates enhance security and add value to properties. Understanding these gates helps in maintaining their efficiency.
Common Issues
Liftmaster gates can face some common problems. Sometimes, the gate won’t open or close. This could be due to power issues. Another issue is the gate moving slowly. This might be due to obstructions or mechanical faults. Sometimes, the remote control might not work. This could be due to battery issues. Regular checks can help spot these problems early.
Importance Of Maintenance
Regular maintenance keeps Liftmaster gates running smoothly. It prevents unexpected problems. Maintenance includes checking the motor and sensors. Cleaning the gate tracks is also important. Lubricating moving parts reduces wear and tear. Regular inspections can identify potential issues. Addressing these issues early can save money on repairs. Proper maintenance extends the gate’s lifespan.

Credit: patch.com
Identifying Gate Problems
Identifying problems with your Liftmaster gate is crucial for maintaining its functionality. This process involves a thorough examination to detect any visible or operational issues. Addressing these problems promptly can prevent further damage and ensure smooth operation. Let’s delve into the key areas to focus on.
Visual Inspection
Start with a visual inspection of the gate and its components. Check for any obvious signs of wear and tear. Look for bent or broken parts, loose bolts, and rust.
- Examine the gate tracks for debris.
- Inspect the gate hinges for damage.
- Look for any obstructions in the gate’s path.
Clean any dirt or debris found during the inspection. Regular cleaning prevents buildup that can affect the gate’s movement. Ensure all parts are properly lubricated.
Operational Issues
Next, identify operational issues that may affect the gate’s performance. These problems can stem from electrical or mechanical faults.
- Test the gate’s response to remote control commands.
- Listen for unusual sounds during operation.
- Observe the gate’s speed and movement.
Check the gate’s motor and control panel for errors. Faulty wiring or a malfunctioning motor can cause operational issues. Ensure the gate is receiving adequate power supply.
Problem | Potential Cause | Solution |
---|---|---|
Gate not opening | Power issue | Check power supply and connections |
Gate moves slowly | Lack of lubrication | Lubricate moving parts |
Unusual noises | Worn parts | Replace damaged components |
By conducting a thorough visual inspection and addressing operational issues, you can keep your Liftmaster gate in top condition. Regular maintenance ensures long-lasting functionality and reduces the need for costly repairs.
Quick Fixes For Common Problems
Having trouble with your Liftmaster gate? This section covers quick fixes for common problems. These solutions can save time and money. Let’s dive into two main issues: power supply and remote control troubles.
Power Supply Issues
The gate may not work due to power supply issues. Here are a few checks:
- Check the power source: Ensure the gate is plugged in. Look for loose connections.
- Inspect the circuit breaker: Sometimes, a tripped breaker can cause problems. Reset it.
- Examine the fuse: A blown fuse can stop the gate from functioning. Replace it if needed.
- Test the power outlet: Plug another device into the outlet. Verify if it works.
If these steps do not fix the issue, consider calling a professional.
Remote Control Troubles
If the remote control is not working, follow these steps:
- Check the batteries: Ensure they are fresh and inserted correctly.
- Reprogram the remote: Sometimes, reprogramming can solve connection issues. Refer to the user manual.
- Clear obstructions: Remove any objects blocking the signal path.
- Test the remote: Stand close to the gate. Press the button. If it works, the issue may be range-related.
If the remote still does not work, it might need replacement.
Dealing With Mechanical Failures
Dealing with mechanical failures in your Liftmaster gate can be frustrating. Understanding the common issues can help you fix them quickly. This section covers two common problems: the gate not opening and the gate not closing. Addressing these issues will help you maintain a smooth and secure gate operation.
Gate Not Opening
If your gate is not opening, check for common mechanical issues. Ensure the power supply is connected and working. A tripped circuit breaker or blown fuse can cause power loss. Here are steps to troubleshoot:
- Check the Power Source: Verify that the gate opener is plugged in and the outlet has power.
- Inspect the Remote Control: Ensure the remote has fresh batteries and is within range.
- Examine the Gate Tracks: Remove any debris or obstructions from the tracks.
- Look at the Motor: Listen for any unusual sounds. This might indicate a motor issue.
Gate Not Closing
If your gate is not closing, several factors might be at play. Addressing these can restore normal operation. Follow these troubleshooting tips:
- Check the Safety Sensors: Ensure they are clean and aligned. Misaligned sensors can stop the gate from closing.
- Inspect the Hinges and Rollers: Lubricate if needed. Stiff or rusty parts can hinder movement.
- Examine the Control Board: Look for any signs of damage or wear.
- Test the Limit Switches: Adjust if necessary. Incorrect settings can prevent closing.
By following these steps, you can address the most common mechanical failures with your Liftmaster gate. Regular maintenance and timely troubleshooting ensure your gate operates smoothly and reliably.
Addressing Sensor Malfunctions
Liftmaster gates are known for their reliability, but even the best systems can have issues. Sensor malfunctions can disrupt your gate’s operation. Addressing these problems ensures your gate works smoothly. Let’s explore common sensor issues and how to fix them.
Sensor Alignment
Proper sensor alignment is crucial for the gate to function correctly. Misaligned sensors can prevent the gate from closing.
- Check both sensors. They should face each other directly.
- Use a level. Ensure both sensors are at the same height.
- Adjust the sensors. Loosen the screws and move them until they align.
- Tighten the screws. Secure the sensors in place.
After alignment, test the gate. The sensors should work without issues.
Sensor Cleaning
Dirt and debris can block the sensors, causing malfunctions. Regular cleaning keeps them clear and functional.
- Turn off the power. This prevents any accidents.
- Wipe the sensors. Use a soft cloth to clean the lenses.
- Check for obstructions. Remove any leaves or dirt around the sensors.
- Turn the power back on. Test the gate to ensure it works.
Regular cleaning can prevent many sensor-related issues.
Adjusting Gate Settings
Adjusting gate settings is crucial for the smooth operation of your Liftmaster gate. This includes calibrating the gate’s limit switches and force settings. Proper adjustments ensure that the gate opens and closes efficiently, without causing any damage or malfunction.
Limit Switches
The limit switches control how far the gate opens and closes. Adjusting these switches ensures the gate stops at the correct positions.
Follow these steps to adjust the limit switches:
- Locate the limit switch screws on the gate motor.
- Use a screwdriver to turn the open limit switch clockwise for a larger opening.
- Turn the close limit switch counterclockwise to shorten the closing distance.
- Test the gate after each adjustment to ensure proper function.
Force Settings
Adjusting the force settings is essential for the gate’s safety. It controls the amount of force the motor uses to move the gate.
To adjust the force settings:
- Locate the force adjustment dials on the gate motor.
- Turn the dial clockwise to increase the force.
- Turn the dial counterclockwise to decrease the force.
- Test the gate to ensure it does not apply excessive force.
Proper force settings prevent the gate from damaging vehicles or hurting people. Always test the gate thoroughly after making adjustments.
Preventive Maintenance Tips
Regular maintenance of your Liftmaster gate can save you time and money. It ensures smooth operation and extends the gate’s lifespan. Below are essential preventive maintenance tips to keep your Liftmaster gate in top condition.
Lubrication
Proper lubrication is crucial for the smooth operation of your gate. Lubricate the moving parts such as hinges, rollers, and chains. Use a high-quality silicone-based lubricant. Avoid using grease as it can attract dirt and debris.
- Lubricate every six months.
- Clean the parts before applying lubricant.
- Check for signs of rust and wear.
Regular Inspections
Conduct regular inspections to identify potential issues early. Look for any signs of wear and tear, misalignment, or damage.
- Inspect the gate’s alignment.
- Check the condition of the wiring and connections.
- Ensure the safety sensors are working.
Perform a monthly check to ensure everything is in order. This simple routine can prevent major problems and ensure the gate operates smoothly.
Use a checklist to keep track of your inspections and maintenance tasks. This helps ensure nothing is overlooked.
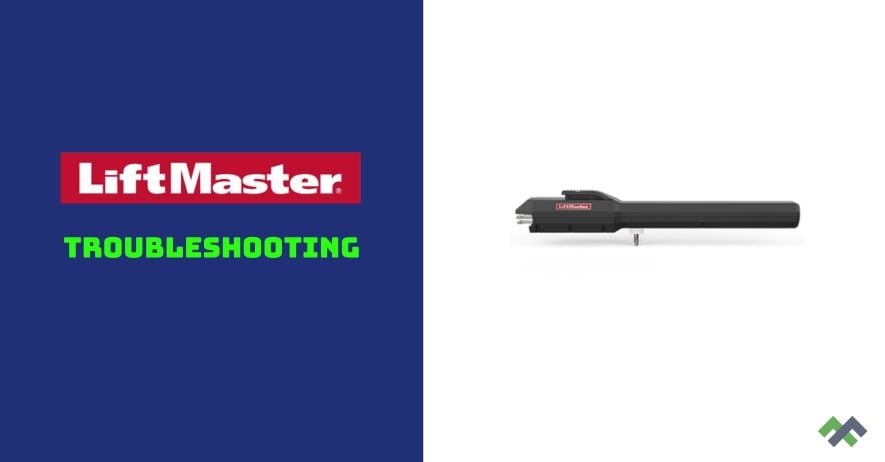
Credit: milwaukeefencefinders.com
When To Call A Professional
Troubleshooting a Liftmaster gate can be tricky. Call a professional if the gate won’t open or close properly. Safety concerns or electrical issues also need expert attention.
Sometimes, fixing a Liftmaster gate can be tricky. You may try to resolve the issue but cannot. In such cases, calling a professional might be necessary. This section will guide you on when to seek expert help.
Complex Repairs
Some repairs require technical knowledge. For example, replacing circuit boards or motors. These tasks involve understanding the system deeply. Attempting them alone can lead to more damage. A professional knows how to handle these parts safely.
Safety Concerns
Working on a gate involves risks. High voltage and moving parts can be dangerous. If you feel unsure, it’s best to call a professional. They have the right tools and safety gear. Their expertise ensures a safe repair process.
“`
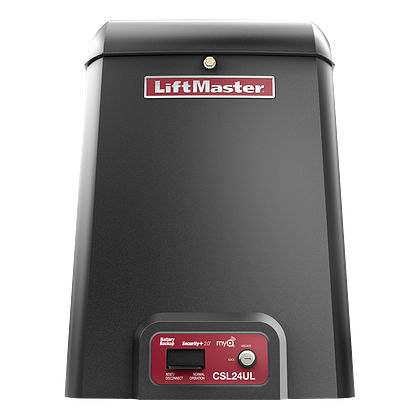
Credit: www.liftmaster.com
Frequently Asked Questions
Why Won’t My Liftmaster Gate Open?
Check if power is on. Look for obstructions. Inspect remote batteries.
How Do I Reset My Liftmaster Gate?
Press the “Learn” button. Hold it until the LED light goes off.
What Does A Blinking Led Light Indicate?
A blinking LED often signals a problem. Check the manual for error codes.
How Can I Test My Liftmaster Gate Sensors?
Place an object in the gate’s path. The gate should reverse direction.
Why Does My Liftmaster Gate Make Noise?
Noises can mean mechanical issues. Check for loose parts or the need for lubrication.
Conclusion
Fixing your Liftmaster gate can be straightforward with the right steps. Regular maintenance helps prevent future issues. Always refer to the manual for specific guidance. Don’t hesitate to call a professional if problems persist. Proper care ensures your gate operates smoothly.
Keep safety in mind during any repair or troubleshooting. Regular checks can save you time and money. Enjoy peace of mind with a well-functioning gate. Happy troubleshooting!